The Canadian automotive supplier Magna in cooperation with the U.S. Department of Energy (DOE) and partners FCA US and Grupo Antolin, has developed a new, ultralight door architecture that achieves the project objective of 42.5% mass savings compared to an average current production door. The goal of Magna and its project partners is to offer a solution for the global automakers to meet emissions standards and reduce fuel consumption through lightweighting.
The engineering team was a collaborative effort between the company’s corporate R&D and various product groups. This combination enabled a full-vehicle perspective on the design of a driver’s-side door resulting in an inventive mix of materials and technology to tackle the challenge of significant weight reduction. This was developed in less than 10 months while keeping the cost within accepted industry parameters and providing a solution that applies to approx. 70 % of the light vehicle market, as the Canadian company told.
“The team started from scratch and reimagined the way we think about the design, development and material-use of a door architecture,” said Swamy Kotagiri, Chief Technology Officer, Magna International. “Building on our significant expertise in lightweighting from previous DOE projects, the team leveraged our broad product-development expertise and tackled this challenge in a cost-effective manner while meeting safety, durability and functionality requirements.”
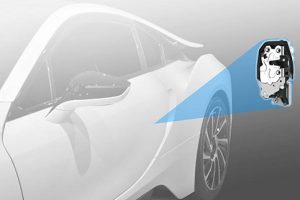
Industry-first electronic door latch selected as a 2016 PACE Award finalist. Source: Magna International Inc.
A key innovation associated with the development of the ultralight door includes integration of a special electronic latch system. This eliminated the need for mechanical hardware and enabled the development of a unique carrier module with integrated glass guides and lift capability of a lightweight hybrid glass laminate, an industry first.
The door-in-white assembly makes extensive use of aluminum, which achieves approx. half of the total mass reduction of the door assembly. Overall, the project applied materials readily available today that can easily be made using existing manufacturing processes, without a significant increase in production costs or changes in body-shop infrastructure.
Grupo Antolin is one of the largest players in the car interiors market internationally. The Spanish company contributed its know-how in the design and manufacture of interior trim components to contribute to the significant mass reduction. The application of advanced molding technologies and polymers contributed approx. 7% to the total mass reduction.
The ultralight door development included intensive simulation efforts, passing all safety and durability testing in the process. The next steps include manufacturing full-scale prototype door assemblies, performance tests and safety tests to validate the design, with the goal of being available for use in production vehicles by the fall of 2020.
The FCA US engineering team has been an integral part of the design and development of the ultralight door, providing engineering collaboration to confirm compatibility with existing assembly operations as well as CAE durability, fatigue and safety analysis. FCA US plans to conduct testing of prototype door assemblies and full vehicles to validate the results of the predictive simulation.