An important feature of plastics is that their properties such as formability, hardness, elasticity, and strength, or temperature resistance can be adjusted with the aid of filling materials. The particle size distribution of a filling material is a decisive factor for the properties of a plastic. A precisely defined particle size distribution is achieved by grinding and subsequent separation, the so-called classification.
The initial layout of the Neuman & Esser air classifier GRC (Guide Ring Classifier) was designed for the classification of roughly 200 μm to 20 μm particles. Depending on the classifier size, throughputs of several tons per hour for medium fineness are possible. For classification in the higher fineness range, throughput is reduced to several hundred kilograms per hour because the number of particles to classify increases exponentially.
The feed material is fed into the GRC from the top using a vertical pipe. After falling onto a distribution plate above the classifier wheel the material is thrown to the outer diameter of this plate. There, the material drops into a ring gap between the classifier wheel on the inside and the air guidance ring on the outside. The inflowing air now carries the particles into the classification zone. Here fine particles are allowed to pass whereas too large particles are being rejected.
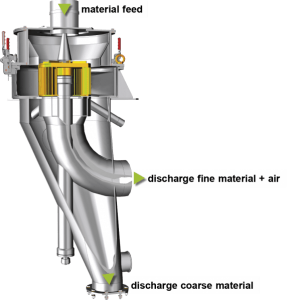
The air classifier divides the feed material into fine material on one side and coarse material on the other side. Source: Neuman & Esser
After passing the classifier wheel the fines leave the classifier housing directly beneath the classifier heading for the downstream filter where the finished product is being discharged from the system. The rejected fraction drops to the bottom of the housing and leaves it via a discharge airlock.
In order to improve the already existing high performance, Neuman & Esser has now made several improvements to the GRC air classifier. The experts focused on how to dispersing fine and coarse in the feed material and on efficiently guiding the material through the GRC classification process.
The new GRC design features now a distribution cone in the inlet of the feed material above a significantly redesigned dispersing unit. After sliding down the cone and passing the dispersion zone, the material reaches the known ring gap. In contrast to the former design now a virtuously engineered guide vane ring handles the transportation into the direction of the classification zone.
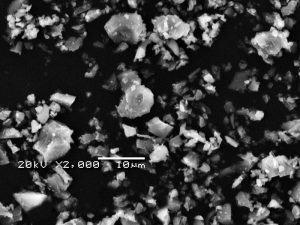
Particle size distribution of filling material using the GRC air classifier. Source: Neuman & Esser
Extensive and detailed testing revealed an unexpected magnitude of improvements not only in yield, throughput and energy consumption but also in the range of achievable fineness, as the company told. The new design now allows widening the possible fineness range from 200 μm to 2 μm.