Recently, Orlin Velev and colleagues show that, in a water medium, liquid silicone rubber can be used to form bridges between tiny silicone rubber beads to link them together – much as a small amount of water can shape sand particles into sandcastles.
Interestingly, the technique can be used in a dry or a wet environment, suggesting that it has the potential to be used in live tissue. The researchers think of an ultraflexible mesh encapsulating a healing droplet, or a soft bandage that can be applied or even directly printed on some portion of the human body.
“There is great interest in 3D printing of silicone rubber, or PDMS (polydimethylsiloxane), which has a number of useful properties”, said Velev, Professor of Chemical and Biomolecular Engineering at NC State. “The challenge is that you generally need to rapidly heat the material or use special chemistry to cure it, which can be technically complex.
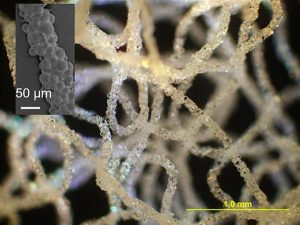
New technique published in Advanced Materials shows the process of 3D printing silicone rubber.
“Our method uses an extremely simple extrudable material that can be placed in a 3D printer to directly prototype porous, flexible structures – even under water”, Velev added. “And it is all accomplished with a multiphasic system of just two materials – no special chemistry or expensive machinery is necessary. The trick is that both the beads and the liquid that binds them are silicone, and thus make a very cohesive, stretchable and bendable material after shaping and curing.”