Soft materials are revolutionizing the way in which we design, utilize, and interact with robots. The last ten years have seen a significant expansion in the field, with advanced applications in implantable and wearable devices, and enhanced human-machine interactions.
In such systems, soft-matter sensors are used to gather information from the environment to carry out a particular task; for example a touchscreen. A plethora of research dedicated to the development of artificial skin technologies has been reported, relying on resistive or capacitive sensing, pressure changes in electrical resistance across fluidic channels embedded in elastomers, piezoelectronics, triboelectricity, optics, and acoustics, among many others. The creativity and ingenuity displayed by researchers in this field is incredible.
While groundbreaking, many of these technologies are not amenable to scale-up due to challenges in their fabrication. Information-rich skins often require delicate materials and wiring for each sensing node, which can understandably become unfeasible on a large-scale.
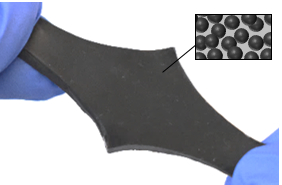
The elastomer composite is loaded with magnetic microparticles to give a soft, tactile skin.
To tackle this problem, a research team led by Professor Carmel Majidi at Carnegie Mellon University has proposed a tactile skin made from a novel magnetic composite, generated from a silicon-based elastomer loaded with magnetic microparticles.
“[We] ultimately want to develop scalable, compliant, and conformal tactile sensing. That means we want to sensorize any surface that needs tactile information e.g., robotic grippers, medical devices, door handles, sports equipment, etc.”, says Ms. Hellebrekers. “Our composite gathers force and contact information but remains in a stretchable, thin format that can cover a variety of complex shapes and surfaces.”
The new skin measures force and local contact through deformation, which changes the position and orientation of the embedded magnetic microparticles with respect to a magnetometer—a device used to measure changes in net magnetic field.
Magnetic field changes and applied force were collected in 25 different grid locations within a 15 mm2 area. Location and depth sensing were carried out using a quadratic discriminant analysis (QDA) algorithm, which was able to distinguish between the 25 grid locations with >98% accuracy. Additionally, to minimize the amount of electronic chips and wiring, the magnetic skin leverages morphological computation properties to reduce the dimensionality of the output before analysis.
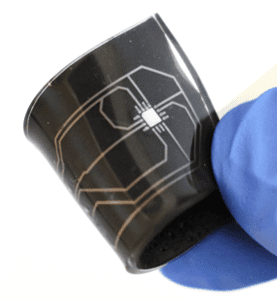
The composite retains the stretchability and flexibility of the host substrate, and is compatible with stretchable circuitry.
“By using a digital chip, we can increase the size of our sensing area without changing the output interface,” adds Ms. Hellebrekers. “The composite needs to be near the chip but is not electrically connected. This allows each application more flexibility in the placement and integration of the magnetic skin.”
As this work is still only a proof of concept, the team envisions improving the range and resolution for force and contact location of their device.
“As with most robotic technology, the next challenge is preserving the quality of signal as we move out of a controlled lab environment and into the real-world. Unanticipated magnetic noise from cell phones and other devices will interfere with the algorithm in its current state. More robust experimentation is needed to handle this type of noise.
This study highlights the need for simple-to-fabricate, information-rich surfaces, enable sensing in areas such as robotic manipulation, soft systems, and biomonitoring.