Carbon fiber-reinforced plastics (CFRPs) are a fast-growing market that have the potential to influence many industries, including the automotive industry. At present, these CFRPs are created through composite manufacturing, a process that is currently evaluated after the fact. This lack of process monitoring and control equipment is hindering the breakthrough of CFRPs into high-volume markets such as the automotive industry.
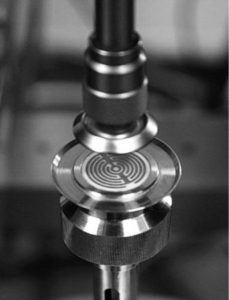
Simultaneous DEA-rheology setup with TMS sensor in fixed bottom plate. The comb-electrode of the DEA-sensor is visible in the center of the bottom plate.
In their study, Alexander Chaloupka and colleagues discuss this challenge and offer a potential solution. By installing a reusable dielectric in-mold sensor, they were able to measure the real-time behavior of the polymers involved in CFRP manufacturing. The sensor installed was crafted to withstand any process influences, including temperature and pressure.
In addition to the physical sensor, the team also used a dielectric analyzer to interpret the data gathered by the sensor in real-time. The presence of this analyzer allowed the researchers to determine critical points in the manufacturing process, such as the minimum viscosity and glass-transition temperature, which are key in predicting the behavior of materials under processing conditions. Predicting their behaviors allows for complex manufacturing techniques and the scaling up of small samples to larger components.
This unique combination of a reusable in-mold sensor and real-time analysis would allow for in-mold quality assurance, as well as contributing to fully automated sensor-based composite manufacturing in the future. CFRPs could break into high-profile industries with the help of this combination, which would aid in controlling manufacturing processes and costs.