Scientists have discovered a new sustainable material that can convert nitric oxide — a smog-contributing gas formed from the combustion of gasoline and diesel — into oxygen and nitrogen at room temperature.
While the exhaust systems of modern-day gasoline vehicles are equipped with three-way catalytic converters that help decompose the pollutants carbon monoxide, hydrocarbons, and nitrogen oxides (NOx) into less harmful gases, the issue is more complex in diesel engines, said Marco Daturi, chemistry professor at the University of Caen Lower Normandy, France.
“The strategy, for many years,” he said, “has been to change the combustion parameters in order to inhibit nitrogen oxide emissions at the expense of particulate formation.”
The standard technologies for removing NOx, such as nitric oxide and nitrogen dioxide, from diesel exhaust are “lean NOx traps” and catalysts. Although these systems are effective at decomposing NOx, they are expensive, complex, and sensitive to temperature and poisoning by other gases that may be present in the atmosphere, including oxygen and water.
Daturi said that developing an efficient catalyst that meets the latest NOx emissions limits is a priority.
To find a catalyst that could potentially outperform existing technologies while remaining sustainable, the researchers looked to nature for inspiration. “Million years of evolution are much more efficient than a few scientists,” Daturi commented.
Mimicking enzymes found in bacteria
Their catalyst design was inspired by the enzyme nitric oxide reductase, found in bacteria, which converts nitric oxide (NO) into nitrous oxide (NO2). The bacteria that produce this enzyme, found in soil, help to keep the Earth’s nitrogen cycle in balance. However, using living organisms as a source of the enzyme is not practical for industry, Daturi said.
“We tried to verify if it was possible to design a material having the same properties of these enzymes, but being solid and resistant,” he stated.
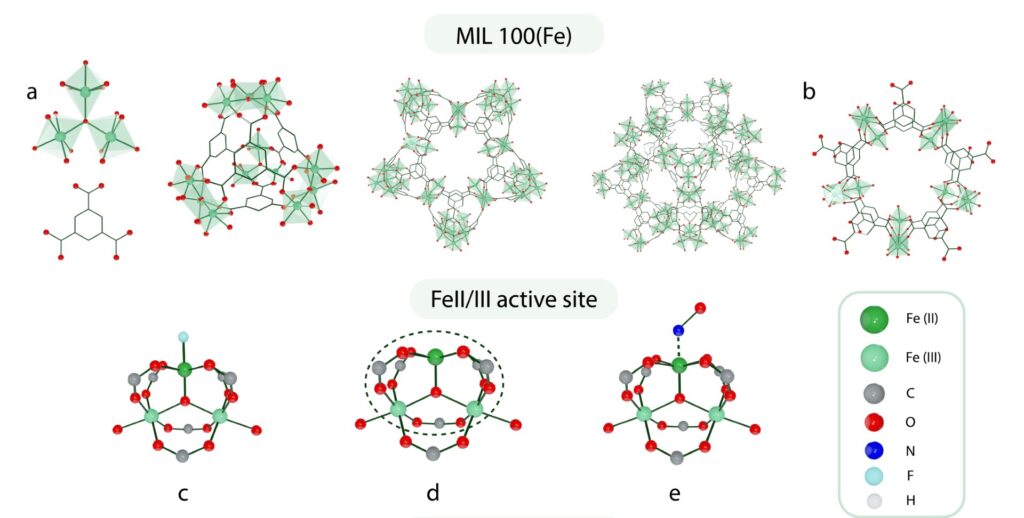
Daturi’s research focuses on metal–organic frameworks, a class of three-dimensional, porous polymers with a plethora of possible structures and compositions. Aside from catalysis, these diverse materials have also been used in dye removal, drug delivery, and carbon dioxide capture, among other applications.
Daturi, along with his colleague Christian Serre, research director at CNRS in Paris, and their collaborators recognized the potential of metal–organic frameworks to mimic the active structure of nitric oxide reductase, which contains two iron ions coordinated with amino acids.
Through computer simulations and spectroscopic studies, they found that a particular iron-based metal–organic framework worked in a very similar way as the natural process. Serre emphasized that preparing the iron-based metal–organic framework catalyst is straightforward, inexpensive, and can be done in several ways.
The easiest route, he said, involves mixing an iron-containing salt with an organic compound in water below 100 °C for two or three days. The product is then filtered, washed, and dried at room temperature overnight.
MIL-100(Fe) catalyst takes shape
The catalyst, named MIL-100(Fe), has two different sites where the reaction takes place: an iron(II) ion and iron(III) ion bridged by an oxygen atom. Both active sites adsorb nitrogen oxide, but only iron(III) converts nitrogen oxide into nitrogen dioxide, becoming reduced to iron(II) in the process.
“At low temperature, when nitrogen oxide and nitrogen dioxide are close to each other, they easily form dinitrogen trioxide, which is unstable in the presence of water, and it decomposes to nitrous oxide and molecular oxygen,” Daturi explained.
Finally, nitrous oxide oxidizes the newly formed iron(II) site into iron(III), releasing nitrogen gas. The active sites are then ready for another catalytic cycle.
“The presence of oxygen and water in the atmosphere is not anymore a problem for nitrogen oxide decomposition — on the contrary, they become necessary for the process,” Daturi said.
He added that their discovery isn’t intended to replace the established nitrogen oxide removal technologies due to the technical and economic considerations of their approach, but it could complement them.
Beyond nitrogen oxide removal, the MIL-100(Fe) catalyst might be well suited for dehumidification and energy-efficient cooling systems due to its large pore volume and affinity for water.
“We have already developed green protocols to scale-up MIL-100(Fe) for industrial-scale production,” Serre mentioned. “We have also contacted potential industrial partners and decision makers to facilitate the development of this technological solution.”
Reference: Marco Daturi, et al., Room Temperature Reduction of Nitrogen Oxide on Iron Metal–Organic Frameworks, Advanced Materials (2024). DOI: 10.1002/adma.202403053