The design limitations and high cost of traditional fabrication process have resulted in a broad interest in fabricating complex metallic microstructures via additive manufacturing (AM). Recently, microscale AM (μ-AM) of metallic structures has been widely explored and different techniques have enabled 3D-printing of true 3D structures. While the main focus of the metal μ-AM community has been focused on achieving small scale structures with complex geometries, in order to enable transition from laboratories to real-world applications it is critical to improve control over the material properties of printed structures.
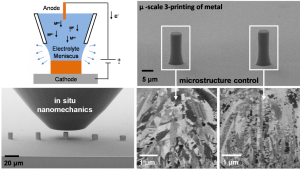
The microstructure of metals 3D-printed using the microscale localized pulsed electrodeposition (L‐PED) process can be controlled in situ during printing.
A new method developed by a team of researchers at the University of Texas at Dallas, termed localized pulsed electrodeposition (L-PED), enables additive manufacturing of pure crystalline metal without any post-processing. Their method has significant advantages compared to the previous processes for patterning and 3D printing of metals.
In L-PED, the microstructure of the 3D-printed metal can be engineered via control over the process parameters in situ during the printing process. Since mechanical and electrical properties of metals are governed by their microstructure, this new capability means that spatial mechanical and electrical properties of the 3D-printed metal can be controlled during the process.
The team, lead by Prof. Majid Minary-Jolandan, demonstrated that through electrochemical process parameters, the density and orientation of the twin boundaries, as well as the grain size can be controlled. Also, the results of in-situ SEM nanomechanical experiments confirmed that such changes in the microstructure directly enhanced the mechanical properties of the 3D-printed metal.
Soheil Daryadel, one of the study’s coauthors, states, “This important advancement eliminates the need for post-processing to engineer the microstructure, which often has undesirable consequences for material properties. L-PED enables 3D-printing of metals with desired material properties, which paves the way for implementing metal μ-AM for functional applications, such as electronic devices, microelectromechanical systems (MEMS), optics, and sensors.”