Two important processing steps for numerous biotechnological and chemical process routes are filtration and extraction. Both require adsorbents with well-defined properties. Materials for these demanding steps have to be chemically stable and they must exhibit high specific surface areas (SBET) as well as open porosities.
Zeolites are microporous, aluminosilicate minerals commonly used as commercial adsorbents. They feature high specific surface areas, but the pore sizes are just a few nanometers. Thus, their application in filtration is limited to gases and small molecules. Ceramic foams on the other hand show high open porosity with tunable pore sizes. However, they exhibit often low specific surface areas, which are disadvantageous for the adsorbents’ efficiency.
Uniform particles so called microbeads and microbead-derived monolithic adsorbents (MAds) combine both advantages of zeolites and ceramic foams. A group of scientists at the University Bremen, Germany successfully prepared silica/alumina microbeads with good specific surface area and porosity.
But sintering of the microbeads was extensive: With heating and cooling, sintering of the samples took 15 hours at 1000°C. In a new study, they applied an easy, inexpensive, and versatile rapid sintering technique using a tube furnace. They determined the specific surface area, pore size distribution, and the stability in different media. Subsequently, they compared the results with material processed by the formally applied sintering method.
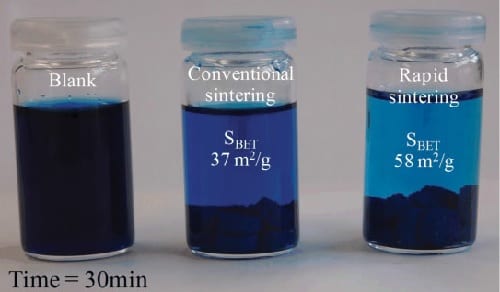
Adsorption tests with methylene blue were conducted to qualitatively show the improved adsorption behavior.
The German scientists showed successful rapid sintering of microbead-derived MAds. The group found a distinct multimodal porosity of the samples for all sintering temperatures. They observed no effect of the holding time on the pore size. But they reduced sintering time from 15 hours to less than 15 minutes. Concurrently, the researchers achieved an increase of the specific surface area in comparison to the old method. This increase was accompanied by a good stability in aqueous media, which was comparable to conventionally sintered MAds. Sintering at 1200°C slightly improved the stability in the tested media hydrogen chloride and sodium hydroxide.