Advanced Engineering Materials has been bringing you the latest breakthroughs in structural materials that are making those important first steps towards commercialization since 1999. With its further increased, record-high Impact Factor of 2.576 (2018 Journal Citation Reports), the journal covers a variety of key topics, such as composites, ceramics, intermetallics, and coatings, and also high-temperature, cellular, and biomedical materials, with a strong focus on new manufacturing techniques.
No access to our published content? Make sure to recommend Advanced Engineering Materials to your librarian. More information can be found here.
In this monthly feature, we highlight the research behind the artwork on the covers of the most recent issue of Advanced Engineering Materials, as well some of the most read Advanced Engineering Materials publications over the last month. These top-downloaded articles are therefore currently freely accessible! Click on the titles below to get to the corresponding papers. You can find this month’s issue here. Also check out our previous Engineering Digest here and here.
Toward functional 3D architectured platform: Advanced approach to anchor functional metal oxide onto 3D printed scaffold
By Junghyun Choi, Patrick Joo Hyun Kim, Jihoon Seo, Jiseok Kwon, Sangkyu Lee, and Taeseup Song
A facile methodology for the fabrication of a metal-oxide-coated 3D scaffold via electrostatic interactions is proposed by Taeseup Song and co-workers at Hanyang University, China. Polylactic acid (PLA) was chosen as the material to be 3D printed for use as a container for the photocatalyst, due to its cost-benefit, for being harmless, and for containing negative surface charges that could be used as adsorption sites for the positively charged catalyst material. Electrostatic interaction was applied to coat CeO2 onto the 3D-printed PLA, and the photocatalytic properties of the scaffold were then tuned by controlling the metal-oxide-particle size. The as-designed CeO2-PLA material presented high photocatalytic degradation performance toward methyl orange. Even after being washed and re-evaluated several times, the scaffold still presented reasonable results, indicating the recyclable nature of the material here prepared, while being also environment friendly and cost-saving.
3D Printing of Highly Stretchable Strain Sensors Based on Carbon Nanotube Nanocomposites
By Mohammad Abshirini, Mohammad Charara, Yingtao Liu, Mrinal Saha, M. Cengiz Altan
Additive manufacturing, commonly referred to 3D printing, has attracted great attention due to its promising potential for rapid prototyping of new materials in complex 3D geometries with precise microarchitectures. 3D printed nanocomposite strain sensors have great potential as flexible and wearable sensors. Yingtao Liu and colleagues from the University of Oklahoma, Norman, OK, USA, present a 3D printing approach to fabricate highly flexible strain sensors using polydimethylsiloxane elastomer and multi‐walled carbon nanotubes based nanocomposites, with a sub-millimeter resolution. The fabricated sensors were applied for the real-time load monitoring of human wrist bending, and show potential for the applications in wearable sensors for human motion recognition.
Broadband and Ultrathin Infrared Stealth Sheets
By Mohammad J. Moghimi, Guangyun Lin, Hongrui Jiang
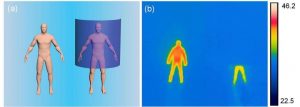
Effect of IR stealth sheets on thermal images of a human model. Color bars represent temperature (°C).
Invisibility is a long-lived dream that has attracted already many scientists to study the behaviour of rendering objects invisible for various light sources. Professor Hongrui Jiang and co-workers have presented a new concept for infrared stealth using silicon nanowires and silver nanoparticles on a flexible, thin substrate to form metallic-dielectric nanostructures. Their technology cannot only be used for small objects, also macroscopic 3D objects can be hidden. The researchers therefore believe that such a breakthrough technology is a significant step toward all-encompassing invisibility technology. For further reading of the full article, please go here.
Solid State Porous Metal Production: A Review of the Capabilities, Characteristics, and Challenges
By Mark A. Atwater, Laura N. Guevara, Kris A. Darling, Mark A. Tschopp
Porous metals have been under development for nearly a century, following two primary routes: liquid state or solid state processing. Process optimization and commercial output has been primarily related to liquid state methods, as solid state processing is often more complex, diverse and with lower throughput. Ongoing advancements in solid state foaming have allowed for a wide array of metals and alloys to be made porous and the three-dimensional structure to be precisely tailored. The extensive variability of pore quantity and morphology makes solid state processes suitable for an assortment of functional and structural applications, with electrodes and biomedical devices being among the most popular in current research. Various techniques for introducing porosity, the way these methods are applied, important considerations, typical outcomes and current applications are reviewed in this article by Mark Atwater and co‐workers.