Researchers in France bring about a big-time improvement that makes dip coating simpler, better, and greener.
Liquid deposition processes are very versatile methods to produce sub-micron homogeneous coatings through spreading of a solution onto a substrate and evaporation of the volatile compounds. They are seen as serious alternatives to dry deposition techniques, such as physical vapor deposition (PVD) chemical vapor deposition (CVD) or plasma-enhanced CVD (PECVD), because they permit endless of chemical combinations to be processed with an excellent control of the inner layer structure and thickness, and with manufacturing rapidity and cost efficiency.
Amongst the various available techniques some are already commonly used in R&D and production, such as dip coating and spin coating. Dip coating is considered as the best technique to precisely and simultaneously control the thickness, the internal (nano)structure, with the highest homogeneity. However, it usually requires a large amount of coating solution to ensure complete immersion of substrates, making it impractical when the solution is unstable and/or hazardous, or contains scare and expensive materials. For such reasons, spin coating is often much more in favor over dip coating, despite the fact that most of the solution is wasted during the former process.
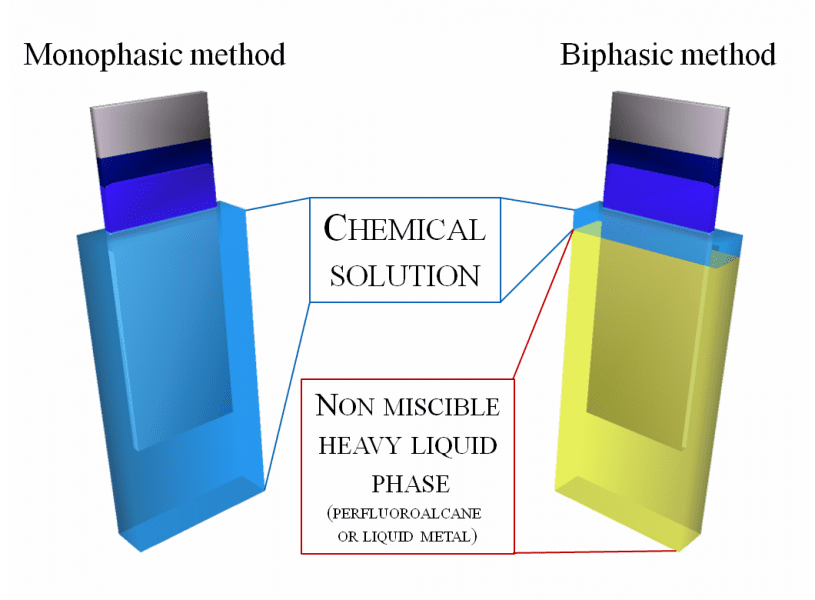
Having worked in the field of liquid deposition processes for the last 20 years, David Grosso has always been motivated to find a new way that combines the high control, the best homogeneity, and the chemical versatility associated to dip-coating with the possibility to coat a single face of a relatively large area substrate with a minimum of solution, and with no waste. Now, D. Grosso and his collaborators M. Faustini and D. Ceratti at Sorbonne Universités and Aix-Marseille Université (both in France) have achieved this goal by developing
A New Dip Coating Method to Obtain Large-Surface Coatings with a Minimum of Solution.
The “bi-phasic” concept is rather simple yet very creative. The researchers introduce an immiscible, heavy, and inert liquid to fill most of the volume of the reservoir before adding the coating solution, and therefore, only a small amount of coating solution is needed to cover the surface of the bottom layer. The substituting phase can be perfluoroalkanes or liquid metals (gallium or mercury) so that the affinity between this phase and the substrate is minimized. In fact, the contact angle at the triple-phase line will be too high to enable any coating by the substituting phase.
The dip coating process using the “bi-phasic” configuration remains the same, where the substrate is withdrawn at a constant speed from full immersion in both phases. Using this approach, the researchers prepare mesoporous titania and silica thin films on glass substrates from sol-gel solutions, and the films are almost identical to those prepared by conventional mono-phasic dip coating. In addition, they also obtain high-quality and large-area single-sided films by selectively wetting only one side of substrates with coating solutions via a syringe, and these coatings include ruthenium dioxide-silica optical absorbers, commercial P3HT conductive polymers, and polymer-based pillar planar nanochannel layers.
This new dip coating method “is quite convenient when tests have to be performed with small quantities of compounds that are too expensive or too difficult to synthesis”, as Grosso says. On the other hand, it comes in handy too “in industrial production where several meter-squares surfaces need to be coated without wasting solutions as it is the case in roll-to-roll coating for instance”. Another inherent merit here is that the bottom liquid phase can be recovered and reused for many times before purification is needed since little contamination is expected. The team is currently working on optimizing their new method, including “selecting the best processing and chemical conditions to reduce to nothing the thickness inhomogeneities, as well as the defects existing at the edges and at the bottom of the substrate (side and drop effects)”.