Material compounds made from plastics and fibers are firmly established in the field of structural lightweight design. Glass and carbon fibers are most commonly used and for example integrated into thin films of thermoplastics as reinforcement. But most of these plastics are based on mineral oil – a rare resource whose extraction and use is harmful for the environment. A more ecological and sustainable approach is taken by the researchers in the Federal Cluster of Excellence MERGE.
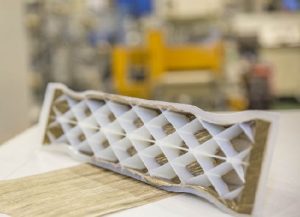
Demonstrator of a bio-based fiber-plastic-compound. Photo: Chemnitz University/Rico Welzel
Ahmed-Amine Ouali, research associate at the Institute of Lightweight Structures explains the approach: “We replace the glass or carbon fiber with natural fibers such as flax. Our plastic matrix is a biopolymer of renewable resources. Thus, the carbon footprint in the product’s life cycle is significantly better.” Also the material characteristics with regard to the structural weight are technically interesting: The use of continuous filaments renders the compound extremely stiff and highly rigid in the direction of the fibers. Furthermore, flax is lighter than glass and cheaper than carbon fiber.
The researcher’s main objective was to develop a procedure with which the so-called semi-finished products made from plastics and natural fibers can be produced on large-scale. Film-stacking-technology is currently common practice. In this procedure, single layers are stacked into a heat press, fused under pressure, removed and further processed into plates in another machine.
For the continuous procedure the MERGE researcher had to design a new rolling mill, a so-called calender. “Natural fibers have a special characteristic in contrast to glass or carbon fibers: they readily absorb fluids. Thus, prior to the processing they have to dry”, as the researcher explains. “At the institute we developed a dryer plant that can be attached to the calender almost without space in between. This way the dried fiber has almost no contact to the moist ambient air.”
“We developed promising, sustainable, durable materials, whose production is significantly more energy-efficient and thus shows a better carbon footprint than in conventional fiber-plastic compounds”, says Ouali. Looking to the future he explains: “We will further experiment with various fiber structures as knitted or non-crimp fabrics, or in other forms and with different matrix combinations for example films or spun-bonded fabric.” That is how MERGE further develops and optimizes the positive material characteristics, ecological factors, and large-scale suitable production procedures.