Polymers present low densities, making them good candidates to replace metallic structures to reduce energy consumption in automotive and aero‐space industry. On one hand, their relative low mechanical properties are mostly addressed by fibre reinforced composites or technical polymers such as poly‐ether‐sulfone, poly‐ether‐imide or poly‐ether‐ether‐ketone (PEEK). On the other hand, their poor surface free energy (γ) leading to insufficient practical adhesion when coated need surface treatment. To prepare their surface for required adhesion, polymer and organic matrix composite surfaces usually undergo several chemical and/or physical treatments. Lately however, for environmental considerations and safety operating conditions, dry‐phase processes are spread to replace usual industrial methods while ensuring adhesion properties.
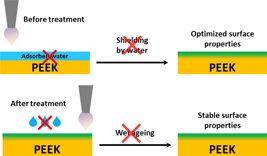
Poly‐ether‐ether‐ketone (PEEK) surfaces have been treated by atmospheric pressure plasma to increase their surface free energies − and hence, their adhesion potential towards metallic coatings as assessed by pull‐off test.
Among all the dry‐phase processes, plasma treatments have long been developed to enhance polymer or composite wettability. PEEK is a well‐known thermoplastic for its remarkable mechanical properties and for its thermal and chemical stability. PEEK is biocompatible thanks to its high chemical inertia, and could be used in biochemical applications such as a substrate for an antibacterial metallic medium or implants with promoted cell adhesion. Moreover, surface metallization is also needed to overcome the poor electric conductivity of polymers, especially for electronic applications.
Nevertheless, the aging of the plasma treatment before coating is critical as several studies report on surface energies which revert to their initial values with time depending on the material and plasma parameters. There are multiple causes of the aging process of which the polymer itself, mainly by its intrinsic surface energy, is an important parameter: this phenomenon of polymeric surface reorganization can be modelled.
A team of researchers from France recently showed that the surface energy of PEEK can be increased using atmospheric plasma activation. The results of their study demonstrate that adsorbed water on the surface plays the role of a shield towards the chemical activation. The removal of the water prior to the plasma activation, by pre‐drying the surface several hours in a dry atmosphere, allowed to attain the maximum efficiency of the plasma activation even if the surface was treated with a lonely scan. Secondly they showed that the intensity of the decrease seems to be dependent on the relative humidity of the storage atmosphere. “We demonstrated that by storing the activated surface in a dry atmosphere, it’s possible to maintain the activation, as suggested by the constant high values of the surface energy after 2 months of aging in a 15% RH atmosphere” says team member Jean-François Coulon. Their research thus shows that it’s possible to maintain the wettability and adhesion towards metallic coatings at high value for a long time by storing the material in a dry atmosphere after plasma activation.