3D printing, in which 3D structures are created layer by layer, has significantly influenced many branches of technology and industry, from pharmacology to electronics. This technique is widely used because it can significantly reduce the time required to create a product without compromising its quality.
4D printing takes this to the next level, where the resulting parts not only have a non-trivial 3D structure but after printing, change their shape or configuration over time.
“4D printing refers to 3D printing of responsive parts that can change their shapes or properties in a programmed way under external stimulations, such as humidity, light, heat, electric fields, magnetic fields, and so on,” said Wenzheng Wu, a professor at Jilin University in China.
“This technique is a novel manufacturing technology, which can save process time, energy and materials,” said Luquan Ren, a professor at the same university. “It can be used to repair equipment in the aerospace industry, such as damage to satellite parts or space stations. Generally, the damage of parts is random, and the size and shape are irregular and not uniform, which often increases the risk of satellite malfunction. This method can be employed to control the shape transformation of the parts, which can therefore be used in space.”
However, these new features bring new manufacturing challenges. So far, the only materials used for 4D printing have been polymers — substances made up of large molecules composed of many repeating subunits — and special shape-memory alloys that deform when cooled but return to their original shape when heated.
“4D printing is currently limited to these two types of materials, which limits its applications,” explained Guiwei Li, a doctor at Jilin University. “Therefore, it is of great significance to break through the restrictions of materials for 4D printing.”
4D printing metallic parts
In order to extend 4D printing to a wider class of materials, Li, Ren, Wu, and their collaborators proposed introducing a laser during the printing process to obtain stronger and more versatile parts.
In their study published in Advanced Science, they were able to achieve a significant improvement upon a technique known as laser powder bed diffusion used in 3D printing in which metal powders are melted and then solidified layer by layer.
“During the usual 3D printing process, residual stresses are often generated due to the high cooling rates and large temperature gradients, which in turn cause processing defects such as delamination, cracks, and deformations,” explained professor Qingping Liu, a co-author of the article. “In contrast, the deformability caused by laser-induced thermal stress can be controlled to reshape 3D printed structures, which can create a new 4D printing method via the laser stimulation.”

In order to produce shape-morphing part with the required mechanical properties, the scientists started with a flat sample of stainless-steel powder. Certain regions of this sample were exposed to a specially programmed sequence of laser pulses, which led to controlled mechanical stress.
Upon subsequent cooling of the sample, this stress is released, leading to the prescribed deformation and the formation of a strong three-dimensional part (see image above).
“The printed parts can realize the shape changing of selected areas during or after forming process due to stress release,” said Wu. “The high-performance, complex metallic shape-morphing structures can be manufactured by this method.”
Using their 4D laser printing technique, the scientists were able to create 14 metallic structures in the shape of a flowers, mimosa, frog tongue, dragonfly, swallow, butterfly, frog, hand, and claw, which, after cooling, acquired the mechanical properties the scientists expected.
While the technology is still in its infancy and the objects the team could print were quite simple, they believe the research is a very important step forward. The scientists expect that their technique will find application in many areas of science and technology, especially in the space and aviation industries. This may be used to repair irregular shell damage with regular spare parts for in-service space stations.
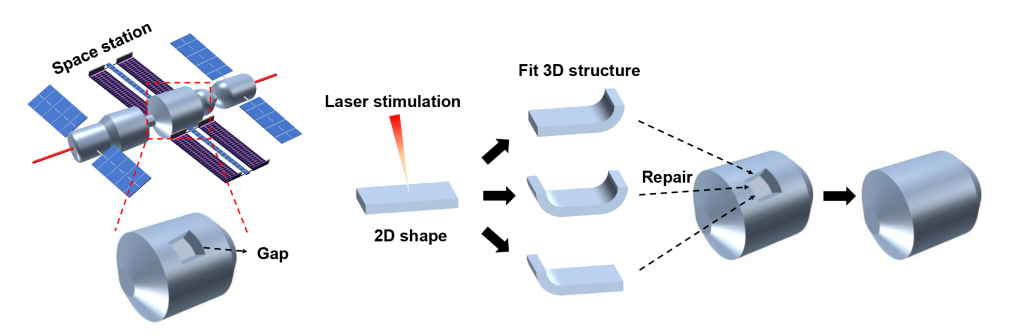
Reference: G. Li et al., “Metallic 4D Printing of Laser Stimulation,” Advanced Science (2023), DOI: 10.1002/advs.202206486.