In order to dimension, design and produce continuously fiber-reinforced multi-layered laminates, a variety of factors has to be taken into account: how many layers are required for the intended load? Made of which materials? And which fiber orientation will be optimal? So far, these factors have been determined by iterations of simulations and experiments, seeing as laminates can be extremely complex compounds uniting laminar layers of quite different materials.
Laminates made from fiber-reinforced plastics and synthetic resins with their high stiffness and low weight are a significant part of today’s lightweight design. Possible applications are everywhere from the aerospace industry to the automotive sector and boat construction.
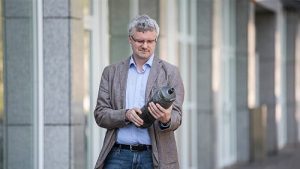
In his research Lars Ulke-Winter creates a algorithm for wound pressure tanks. Photo: TU Chemnitz/Rico Welzel
Dr. Lars Ulke-Winter from the Department of Lightweight Structures and Polymer Technology from Chemnitz University of Technology has written his PhD thesis on the solution of this difficult optimization problem in the structuring of laminates: his model was taken from nature, namely ants.
“I work with methods analogous to nature. So I will abstract from the ants’ swarm behaviour and develop an algorithm based on it that’s suitable to solve the problem”, Ulke-Winter explains. “Let’s assume an ant colony is looking for the best possible way towards a source of food and let’s further assume that every single ant has to make ten decisions on their way: right or left. If one path turns out to be shorter, i.e. better, the ant will leave a stronger track of pheromones, so that the other ants will choose this path more often. From this thought process I have come up with an algorithm”, Ulke-Winter continues.
The ants’ food equals the laminate one is trying to produce. The path towards it including its ten decision equals the ten laminate layers. “I use virtual ants for my simulation, trying out different paths, i.e. different layer structures. The next calculation goes backwards from the layers to finding the respective stiffness of the layer piles, concluding in a virtual pheromone trace for the respective quality of the layer structure. More and more ants from the virtual colony will follow this trace.” Thus, bit by bit the optimal path, i.e. the optimal laminate will emerge.
Using such a nature-based optimization method is not really novel at all, but applying it to laminates in this way is Ulke-Winter’s original idea. He turned it into a program that doesn’t need more than the amount of layers and the required load in order to swiftly calculate the optimal orientation of all layers in the laminate. “In addition, the program can optimize the material for each layer and you can vary the amount of layers by changing the number of iterations”, Ulke-Winter adds.
Another part of his PhD thesis focused on applying this algorithm to wound pressure tanks. Their windings can have varying orientations as well. Just enter the fiber strength and the production parameters of the machine and you will get the optimal ratio of cross-winding and surface winding around the core in order to keep the weight light.
Ulke-Winter gladly makes his optimization algorithms available to his colleagues at the Federal Cluster of Excellence MERGE as a design tool. Calculating and optimizing lightweight structures is at the core of the cluster’s Research Domain “Modeling, integrative simulation and optimization”. With this method the researchers can work towards the overall objective of producing high-strength and lightweight materials and components much more efficiently and without any waste of materials.