The poor flowability of fine powders in chemical and pharmaceutical industries can lead to the clogging of apparatuses, longer maintenance times, precious product losses, and possibly even to the partial destruction of plant. Such clogging mainly stems from van der Waals forces, which increasingly dominate over gravitational and coulomb forces when surface area increases, and interparticle distance decreases with smaller particle size. To overcome poor flowability in industrial systems, nanoparticles known as gliders, flow agents, or flow regulators are used to increase the interparticle distance and decrease van der Waals forces.
Because flow agents have to be distributed as homogeneously as possible to reach higher flowability, a costly mixing process is necessary. Although improved over the years, this mixing process is carried out batchwise and takes from hours to days until the desired mixing quality, and hence flowability, is reached. If this process could be carried out continuously, the cost of production could be significantly reduced and product quality better controlled.
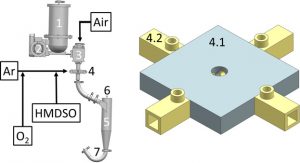
Dielectric barrier discharge setup used for the treatment of lactose powder. 1: storage tank; 2: screw conveyor; 3: funnel, 4: quadrojet assembly with 4.1: ground electrode and 4.2: dielectric barrier channels; 5: cyclone; 6: dip pipe and exhaust gas outlet; 7: powder collection tube
A team of researchers from the Institute of Process Engineering from Switzerland showed for the first time that the enhancement of powder flowability from the cohesive to the easy flowing regime in a continuous process at atmospheric pressure is possible using a dielectric barrier discharge. This technology could replace the time‐consuming batch processes currently used in industry.
The team used a plasma jet‐like setup that can produce substantial amounts of silica‐like nanoparticles. The technique is a promising way to create flow agents for the treatment of powders. The jet‐like setup is adapted by arranging multiple jets around a middle tube through which powder can fall.
“The aim of this work is the creation of nanoparticles and subsequent deposition onto the surface of fine‐grained powder to enhance flowability. This technology could replace the time‐consuming batch processes currently used in industry” according to team member Roger Wallimann.