It would have been hard to miss the 3D printing and additive manufacturing (AM) boom that has swept the world in the past few years. A plethora of new technologies have been developed alongside advancements to pre-existing ones. These developments trend toward more intricate, more precise, and more controllable printed products for use in a wide variety of fields.
A relative newcomer to the 3D printing space is melt electrowriting (MEW), which was pioneered by Professor Paul Dalton and Professor Dietmar Hutmacher in 2011. MEW utilizes an electric field uniquely coupled with AM technology for the controlled deposition of a molten polymer jet, which rapidly solidifies into a fiber. These submicron fibers can be consistently laid on top of each other, resulting in the ability to direct-write complex and multi-scaled architectures and structures, and overcoming the resolution challenge that a majority of other additive manufacturing technologies encounter.
In a recent Advanced Functional Materials review, Thomas Robinson, Professor Dietmar Hutmacher from Queensland University of Technology, and Professor Paul Dalton from the University Clinic Würzburg outline the developments in the MEW field over the last four years. These include progress in scale-up, digitization, and expanding the library of compatible materials, showing that MEW will become a disruptive AM technology in the near future.
“The rapid development of MEW in the past four years is simply breathtaking – there is no other way of describing the number and diversity of advancements in this field,” says Dalton. “The [printomics] technology allows for a superb testing environment that will likely transcend to other additive manufacturing technologies in the near future,” adds Robinson.
Their review provides a comprehensive overview of recent MEW advancements for applications ranging from drug delivery and biomedical applications, to soft sensors and flexible electronics, and further into the area of microfluidics. Some exciting developments include vertical printing on a double-sided collector, which could allow easier translation to scaled-up industrial applications, as well as digitization for high throughput analysis of printing parameters.
The control and tailorable properties afforded by MEW are of particular interest in scaffold guided tissue engineering where the “quest is not to replicate [or] copy the physical structure of the tissue,” says Hutmacher, co-author and a leader in MEW research, “[…] but to guide the regeneration process by designing a scaffold architecture.”
As automation and stabilization are introduced and optimized, the groundwork is laid for MEW to become a disruptive technology worth keeping a close eye on in the near future.
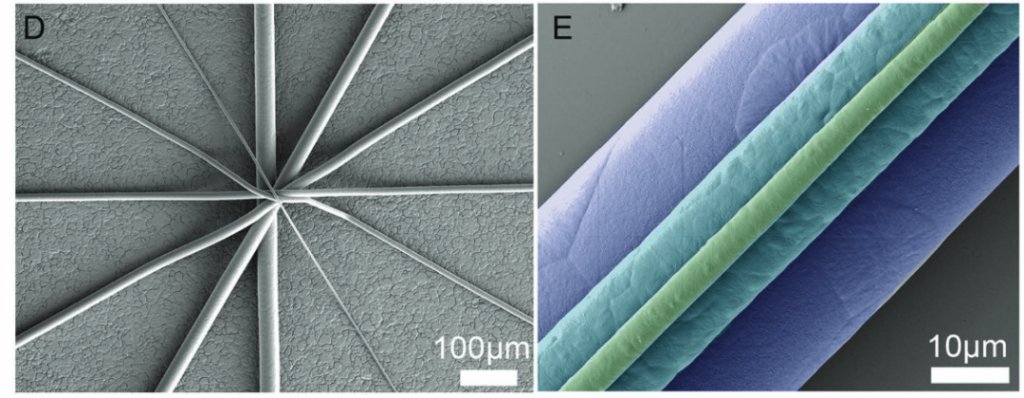
Scanning electron microscope images of various melt electrowritten scaffold designs.