Whether producing engine parts, turbine blades or hip implants: Regarding forged parts, the material is the main component of the production costs, especially if a high duty material like titanium is used. During a new research project, the Institut für Integrierte Produktion Hannover (IPH) aims to develop a process in which less material is needed and which, at the same time, decreases time and energy consumption. This way, the researchers try to reduce the overall production costs significantly. Small and middle-sized forging enterprises in particular will benefit from the results.
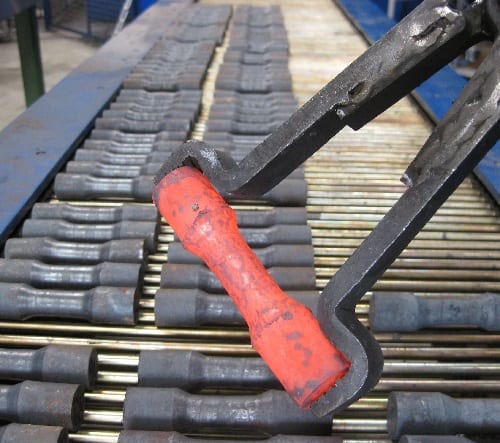
Forged preforms created by using cross wedge rolling must be further processed in order to obtain the final shape. Source: IPH
Die forging is forming of hot metal. To produce complex heavy duty parts, a single forging step is not enough to realize the complex shape. Therefore, so called preforms are produced during the forging process. To produce these preforms, different techniques are used. In most of the processes much of the material gets lost: e. g. during machining a lot of excessive material is gradually removed.
Cross wedge rolling (CWR) is the most efficient way to produce preforms. In this process the hot metal is formed into shape while rolling. The material utilization in cross wedge rolling is up to 100%. Also, less time and energy is needed, compared to machining. A lack of knowledge about the design of a cross wedge rolling process in general and especially for titanium and stainless steel is a seriousproblem for the European forging industry. But particularly for these expensive materials an efficient material utilization has a great benefit.
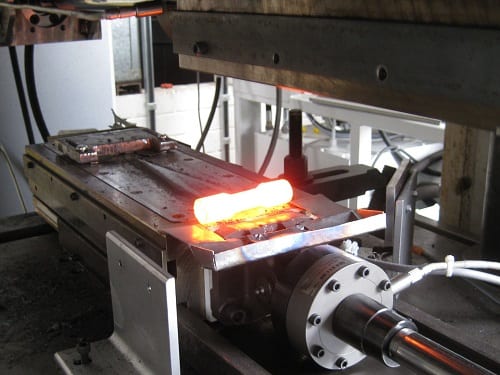
Cross wedge rolling in action at IPH: As part of the research project “CoVaForm” a similar machine will be constructed and built, designed specifically for titanium hip implants. Source: IPH
To examine the cross wedge rolling technology, a titanium hip implant will be forged in the research project “CoVaForm”. The IPH has gained a lot of experience in cross wedge rolling during several research projects and will now build up a new CWR machine to produce preforms for a hip implant. This CWR machine will be tested at a collaboration partner by the middle of next year.
Funded by the EU, “CoVaForm” started January 1st 2014 and will last for a period of two years. The shortcut stands for “Conservation of valuable materials by a highly efficient forming system”. The project consortium consists of four enterprises and three research institutes from Germany, Spain, Italy, Austria and Turkey. This project is financially supported by the European Union as part of the seventh framework program (RP7).