Dry reforming of methane has attracted much interest from both research and industrial communities because, in addition to the production of synthesis gas (syngas) – a fuel gas mixture mainly used for electricity generation – the utilization of CO2 itself can reduce greenhouse gases. Moreover, the generated syngas can be utilized as a reactant for the synthesis of eco‐friendly chemicals and clean fuels. Relative to the steam reforming process, dry reforming of methane is a more suitable technology for the production of oxygenated chemicals.
Conventional dry reforming of methane has been investigated for decades, but it has not been widely implemented on a commercial scale, partly because of the high cost of reaction and because of the persistence of severe coking. Recently, plasma has been explored as a promising tool for dry reforming processes. Most of the investigated plasma sources are non‐thermal, but thermal plasma sources can provide highly thermal environments, which are beneficial for endothermic reactions.
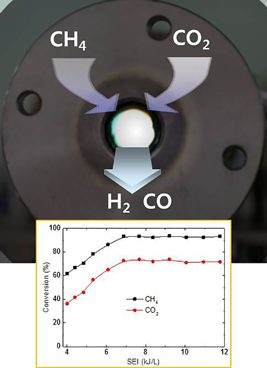
An energy efficient dry reforming process using a rotating arc plasma.
Researchers from the Korea Institute of Machinery and Materials investigated the dry reforming of methane using an AC rotating arc: in short, the dry reforming can be done with high efficiency and low energy cost compared with other plasma sources. Because of the novel long nozzle design, the system can maintain a constant arc length across a wide plasma power range, leading to a high thermal energy efficiency of 76% during methane reforming. In addition, by optimizing the CH4/CO2 molar proportion and the SEI conditions of the AC rotating arc plasma, the energy cost for syngas production is at least 20% lower than the lowest energy costs reported to date. Notably, the conversion of CH4 and CO2 reach almost 100%.
“Overall, we believe that the results presented herein are of great interest to a wide range of industrial applications that require high thermal energy efficiency, low energy cost, and high gas conversion” says team member Dae Hoon Lee.