Technology has always been limited by the capabilities of available materials. Metamaterials show promise for advancing technology by enabling unnatural behaviors that are derived not just from their composition, but from their micro-architecture and, even more recently, active control.
Metamaterials that can locally control their stiffness and shape would enable a host of new technologies, including airplane wings that actively eliminate vibrations, improve maneuverability, and decrease fuel consumption in dynamic flight conditions.
At the University of California, Los Angeles, Dr. Jonathan Hopkins and his team have recently reported a metamaterial comprised of low-melting temperature metals embedded in elastomeric spheres, the phase of which can be controlled via uploaded instructions.
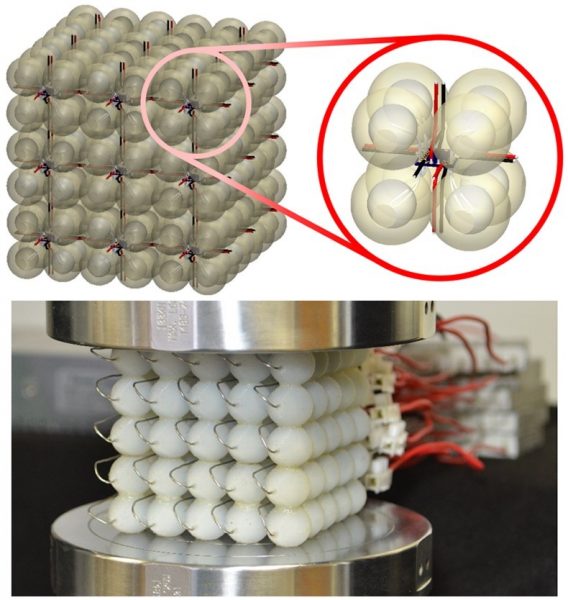
To demonstrate the feasibility of this concept, the team built a macro-scale cubic lattice of gallium-filled silicone spheres. Wires threaded through each row of spheres allows an applied electrical current to melt the gallium cores. While the lattice experienced a 3.7x reduction in stiffness at 7% strain once all of the gallium is melted, simulations illustrated that much larger changes in stiffness are possible when the metamaterial has thinner silicone shells or undergoes larger compressive strains.
Previous approaches towards making tunable stiffness metamaterials have used a variety of actuators, buckling elements, and similar phase-changing metals, but Hopkins points out that those concepts either cannot locally change stiffness at select locations or they don’t change stiffness as drastically as the concept proposed here.
“We are entering an age where metamaterials will lay the groundwork for next-generation technology,” he says. “Materials like ours will open doors to new developments that will take us in the right direction.”
Kindly contributed by the authors.