Glass can be molded, formed, blown, plated or sintered. Its formal qualities are closely tied to techniques used for its formation. From the discovery of core-forming process for bead-making in ancient Egypt, through the invention of the metal blow pipe during Roman times, to the modern industrial Pilkington process for making large-scale flat glass; each new breakthrough in glass technology occurred as a result of prolonged experimentation and ingenuity. Each time it has given rise to new possibilities for versatile applications of the material.
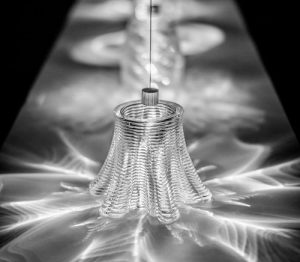
The Mediated Matter Group together with MIT’s Department of Mechnical Engineering and MIT’s Glass Lab developed a glass printing process
Now, the Mediated Matter Group in collaboration with MIT’s Department of Mechnical Engineering and MIT’s Glass Lab developed an optically transparent glass printing process. The so called G3DP is an additive manufacturing platform designed to print optically transparent glass. The tunability enabled by geometrical and optical variation driven by form, transparency and color variation can drive; limit or control light transmission, reflection and refraction, and therefore carries significant implications for all things glass.
The platform is based on a dual heated chamber concept. The upper chamber acts as a kiln cartridge while the lower chamber serves to anneal the structures. The cartridge operates at approximately 1900°F (1040°C) and can contain sufficient material to build a single architectural component. The molten material gets funneled through an alumina-zircon-silica nozzle.
The project synthesizes modern technologies, with age-old established glass tools and technologies producing novel glass structures with numerous potential applications.