Chemicals and fuels enabled by solar power have taken the research world by storm over the past decade. The idea of using heterogeneous photocatalysts to generate hydrogen from water and convert carbon dioxide in the gas phase into a variety of chemicals and fuels has wide reaching implications for the future of the global chemical and petrochemical industries.
After an exciting decade of research, a new generation of solar fuels start-ups are coming out of the woodwork, but are together facing a number of challenges when it comes to photonic efficiency, scale-up and product development.
Our aim with this opinion editorial is to air these challenges in broad daylight for CO2 as a renewable carbon resource, so together as a solar fuels community we can move towards cleaner, less wasteful, and more equitable chemical and fuels process industries for all.
To amplify, sunlight can power the transformation of CO2 to synthetic fuels in two main ways. One employs sunlight “indirectly” to produce electricity, which enables electrochemical, photoelectrochemical and biochemical reduction of CO2. The other uses sunlight “directly” to facilitate thermochemical, photochemical and biochemical reduction of CO2. The reducing agent is gaseous or liquid water or hydrogen.
The roughly 100,000 chemicals produced industrially worldwide are made from about 10 raw materials, including fossil derived petroleum, natural gas, coal, and biomass (as well as rock salt, phosphates, sulphur, air, and water). In the same way these feedstock’s once replaced the use of coal tar as the principle chemical feedstock, trading these in for ever-present greenhouse gases can help usher in the next generation of chemical processes.
Further, traditional, thermally-driven heterogeneous catalysis has been the backbone of the chemical industry for over a century and is responsible for 90% of all chemicals produced worldwide. As such, it makes sense that we would continue to use this successful technology and improve on it by not only trading in the conventional feedstock for a sustainable one, but also trading in its main source of energy from fossil fuel combustion, to solar activation. But how can we make it happen?
A community that hitherto touted the benefits of being able to “have your cake and eat it too” with CO2-derived solar fuels, is now being faced with the cruel realities of chemical engineering in which this platitude doesn’t exist, and “greening” an industry in no way trumps thermodynamic and economic analyses.
Two new start-ups taking on this challenge have recently come out of the woodwork: The Solistra Corporation and Dimensional Energy are paving the way towards this new future with three fundamental questions: How do we optimize photonic efficiency, how should we scale and what should we make?
Decoupling these is not straightforward. To achieve high conversion efficiencies of photons to fuels, ideally you need to optimize the capture of incident photons by the photoactive sites of the photocatalyst strategically located within the photoreactor.
The product you choose to make and the scaling strategy you adopt both affect the economic viability of the process, and create a chicken-and-egg dilemma for would-be business-starters. Many CO2 conversion ventures are now developing “modular” plug-and-play units, however, if your goal is to make commodity chemicals, the general philosophy is that in order to obtain the best economics, scale is your friend. You must build the biggest plant possible, and the heterogeneous catalysis industry has delivered this ability.
Competing electrochemical CO2 conversion processes have high water, energy and economic demands and have been historically reserved for the production of “specialty” chemicals priced up to USD 1000/kg.
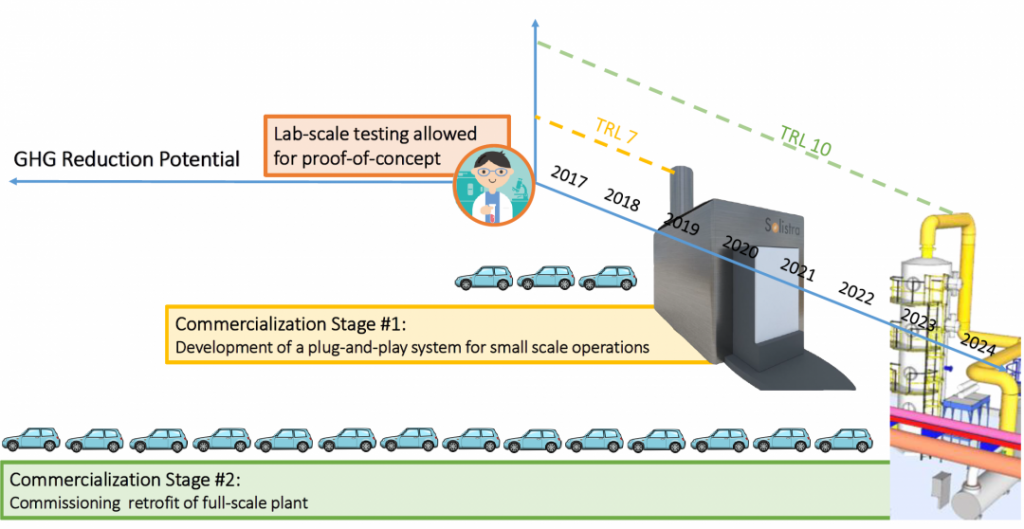
Figure 1. Transitioning gas-phase heterogeneous CO2 photocatalysis from basic-directed laboratory science technology readiness level TRL 1 to proven and readied modular units and large-scale systems for full commercial deployment TRL 9. Illustration courtesy of Alexandra Tavasoli, Solistra Corporation.
On the other hand, a large plant comes with a high price tag, and although this seems more capital intensive, the end product is (hopefully) less capital intensive than if you had built a small modular unit. As well as securing the funds to build a full-scale plant is more complicated due to the larger financial risk than pitching a mass-manufactured, off-the-conveyor-belt modular chemical process.
Scaling gas-phase heterogeneous photocatalysis processes is no easy feat. The obvious issue of the intermittency and tracking of sunlight is only the beginning. None of this can come to fruition unless the so-called “heart” of a traditional chemical plant, the reactor, is giving rise to a new era of photocatalyst and photoreactor innovation, a truly interdisciplinary challenge that crisscrosses the borders of the chemical, materials, optical, electrical and mechanical engineering sciences.
A potential research, development, demonstration and deployment technology pipeline to bring heterogeneous CO2 photocatalysis to market is illustrated in Figure 1. It requires a transition of the basic-directed science technology readiness level TRL 1-2 to the engineering of high photonic efficiency photocatalysts and photoreactors, representing TRL 3. This is pivotal for advancement to lab-scale proof-of-concept prototypes TRL 4, testing-validation for small-scale semi-integrated laboratory prototypes TRL 5, verification of prototypes TRL 6, demonstration of integrated pilot systems TRL 7, incorporation of modular and large-scale units into a commercial design TRL 8, culminating with proven and readied systems for full commercial deployment TRL 9.
Parallel pipeline developments include, techno-economic analyses of mass, energy and economic flows, technological, regulatory and market risk analysis, and greenhouse gas mitigation impact.
The field is poised around TRL 5-6, an achievement which bodes well for a solar fuels technology TRL 9 that can deliver on its promises in the next 5-10 years!
Written by:
Alexandra Tavasoli, Thomas Wood and Geoffrey Ozin
Solar Fuels Group
Solistra Corporation