Cement is one of the most widely used building materials in the world due to its low cost and longevity. While its usage is only increasing, its production is one of the world’s leading contributors of CO2 emissions, with 2.8 gigatons produced each year.
Action to curb these emissions through alternative production methods or substitute materials are currently being explored by researchers around the world, though none have come close to reproducing cement’s desirable qualities.
Now, researchers from the University of Colorado Boulder have combined sand, a hydrogel, and bacteria into a living material that has similar strength to cement-based mortar, as well as the ability to carry out biological functions.
“Microorganisms can be leveraged for multiple purposes in the design of [living building materials], including increasing the rate of manufacturing, imparting mechanical benefit, and sustaining biological function,” said the authors in the study.
The team used a 3D sand–hydrogel scaffold that they inoculated with Synechococcus sp. PCC 7002 (Synechococcus) — a photosynthetic cyanobacterium that converts CO2 to sugars during photosynthesis. Cyanobacteria are well known to survive extreme environmental conditions, including high and low temperature, salinity, and humidity, making them ideal candidates for living materials.
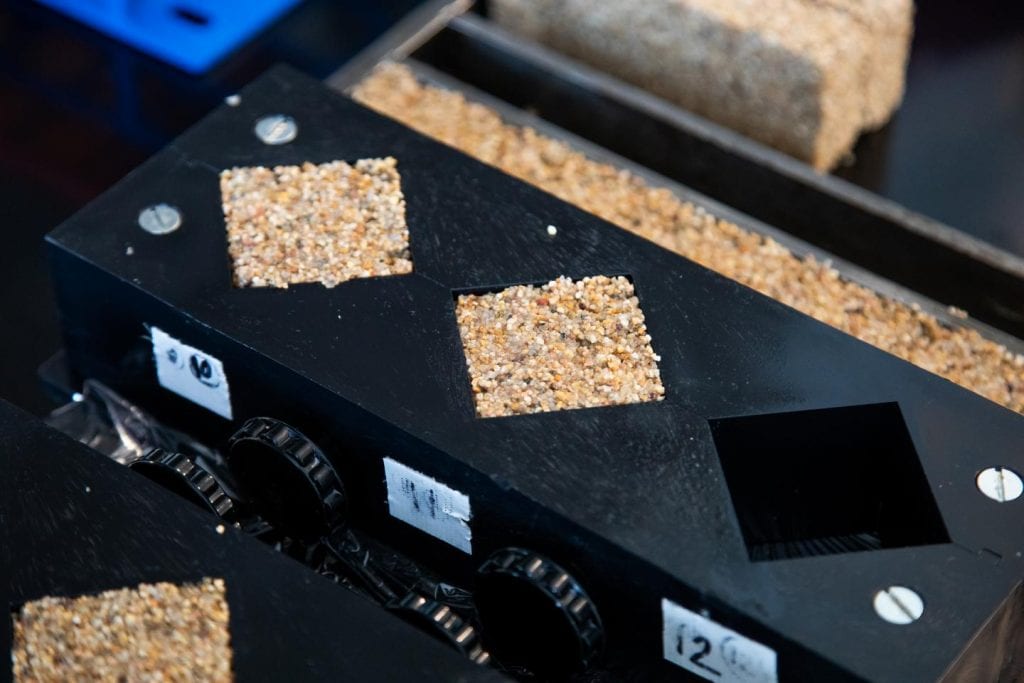
“We use photosynthetic cyanobacteria to biomineralize the scaffold, so it actually is really green. It looks like a Frankenstein-type material,” said senior author Wil Srubar, who heads the Living Materials Laboratory at the University of Colorado Boulder. “That’s exactly what we’re trying to create — something that stays alive.”
These new materials are also capable of being regenerated from one parent “brick” using temperature and humidity switches. This corresponds to cycles of incubation at 37 °C, followed by low-temperature storage, where the gelatin matrix solidifies and encapsulates the bacteria.
Splitting one brick in half and extending its shape using additional sand and hydrogel scaffolding, Sruber and his co-workers demonstrated the creation of eight new bricks (three successive generations) from a single parent. According to Sruber, this will no doubt shift the way in which we think about current manufacturing practices and how we re-use materials.
“From an engineering perspective, the responsiveness of [living building materials] to these temperature and humidity switches is opportune. Material systems that protect microorganisms with encapsulating gels or other solid media generally require physical damage to the encapsulant in order to trigger additional biomineralization,” the authors said. “While this approach may be appropriate for in situ crack sealing, it is challenging to elicit a uniform metabolic response from embedded microorganisms. By contrast, environmental switches can be applied uniformly to precisely control microbial activity.”
However, a trade-off exists between biological viability and mechanical performance because the gelatin gains its maximal strength when dehydrated and the bacteria requires humidity to function. A balance between these two factors was required for this class of living building material, but the researchers believe that the process could be optimized by exploring the use of additives to enhance bacteria tolerance to dry conditions.
Although this technology is still in its infancy and is not intended to completely replace cement completely, it represents a new frontier in material manufacturing: a new class of responsive materials “in which structural function is complemented by biological functions.”
“This is a material platform that sets the stage for brand new, exciting materials that can be engineered to interact and respond to their environments,” said Srubar. “We are just trying to bring building materials to life, and I think that is the nugget in this whole thing. We’re just scratching the surface and laying the foundation of a new discipline. The sky is the limit.”