There is a growing occurrence of heart problems in the global population, especially cardiac arrhythmias in which the heart beats outside of its usual rhythm. Not all irregular heartbeats are serious though some can lead to more fatal outcomes, such as stroke or heart failure. In the US alone, it’s predicted that there will be an increase from 3 million cases of cardiac arrhythmia in 2020 to 6 million in 2050. As numbers rise, so too does the demand for operations to treat these afflictions.
In conventional procedures, a surgeon creates a small incision and inserts a thin catheter into the patient’s artery. They then turn to a large device nearby and guide the device through, deftly steering it to the heart. How will this story ends depends on many factors, including the device in use.
To improve on the safety and success of these operations, researchers from the École Polytechnique Fédérale de Lausanne together with the Eidgenössische Technische Hochschule Zürich and The University of Electro-Communications Tokyo have created a dexterous variable stiffness catheter composed of smart threads that can be guided remotely.
Ablation surgeries require bending catheters in a wide variety of directions to position the tool appropriately for its task. However, an externally-generated magnetic field, commonly used to guide conventional remote catheters, is typically confined to a single direction, making navigation tricky and increasing the duration of the procedure.
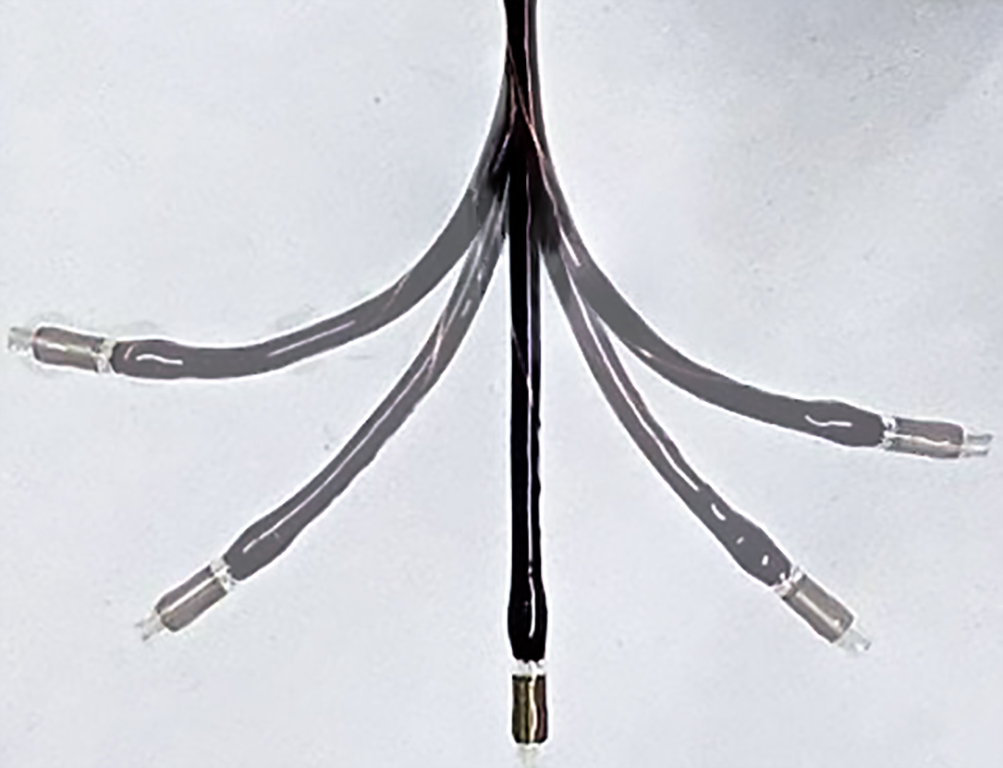
To address this problem, segmented catheters composed of individual smart threads made of a conductive shape memory polymer were created. The material is nontoxic and can reversibly change its stiffness in response to temperature changes, converting between rigid and soft states. In a rigid state, it can locally resist the magnetic field and increase the dexterity of the catheter. Reverting to a more soft state allows it to navigate the delicate arterial system, minimizing damage and easing movement.
These smart devices were made using a new fabrication method consisting of a dipping technique, which involves coating polymer tubes by dipping them into a tank containing the material. This technique enables the manufacturing of threads with the desired electrical properties and thickness down to a few tenths of a millimeter.
In addition to the application of very constrained procedures, such as surgery, the size, stiffness, and resistance of these new threads can be easily tuned for different applications due to the scalable fabrication process. These include incorporation into robots to achieve different locomotion modes or developing smart clothing by weaving these threads into fabrics. Perhaps these smart clothes might help a person lift heavier objects, run longer, and better sense their environment.
Despite their wide potential, these threads still have room for improvement. In future, we hope the threads and their fabrication process can be further optimized to achieve faster reaction times and the ability to translate to industrial batch fabrication.
Reference: Yegor Piskarev, et al., A Variable Stiffness Magnetic Catheter Made of a Conductive Phase-Change Polymer for Minimally Invasive Surgery, Advanced Functional Materials (2022). DOI: 10.1002/adfm.202107662
Disclaimer: The author of this article participated in the study