3D displays are state-of -the-art technology. For example, we can think of stereo displays capable of conveying depth perception to the viewer. In nature, we can consider the cephalopods – a class of marines animals, which includes the squid and octopus – in which live 3D displays have existed for hundreds of millions of years. These marine animals have the incredible ability to morph the structure and pattern of their skin, creating shapes and textures for camouflage or controlled motion.
Now, a research team from the University of Iowa and the University of Illinois at Urbana-Champaign is developing a smart skin inspired by cephalopods, which can be used as interfaces in 3D displays for the visually impaired, as well as to help reduce drag on marine vehicles.
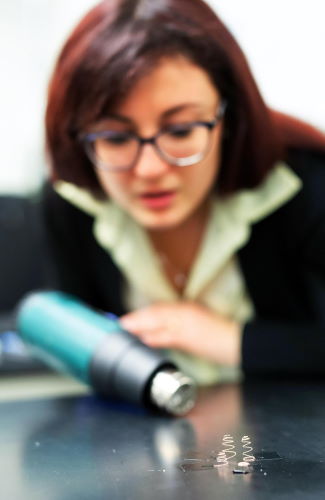
Professor Caterina Lamuta of the University of Iowa, as well as Professor Sameh Tawfick and Professor Nancy Sottos of the University of Illinois at Urbana-Champaign, used twisted and coiled polymer fibers to imitate cephalopod muscles. Thus, producing an artificial, lightweight skin that is capable of fine motion and shape modulation
“Our society and scientific community seek the development of new adaptive smart materials systems for a wide range of applications ranging from the military field to medical and leisure applications,” said Professor Lamuta. “The unique mechanisms of living organisms represent an invaluable source of inspiration for the design of lightweight, reliable, adaptive, multifunctional, and efficient materials systems. The inspiration for this work came from cephalopods and their extraordinary ability to perform texture and shape modulation.”
Cephalopods change their skin with dermal erector muscles, called papillae, to take on new shapes and textures in a fraction of a second. The researchers mimicked the animals’ papillae and created a new skin based on digital texture voxels (DTVs) using twisted spiral artificial muscles (TSAMs) from thin polymer and copper fibers. “With only 0.2 V/cm, TSAMs are able to provide a stroke up to 2000% and a potentially unlimited number of target textures and shapes, if several TSAMs are embedded into a soft material and individually actuated,” Professor Lamuta explained.
In their work the researches also provide a theoretical model to explain the actuation mechanism of TSAMs, due to internal joule heating and untwisting of the anisotropic polymer fibers. Now, a specific vertical displacement can be tailored for each TSAMs to design specific output textures and shapes.
Professor Lumata adds that “contrary to conventional electric or pneumatic actuators, which require heavy, bulky, and noisy power sources, TSAMs can be electrically actuated with a small input voltage and pave the way for the development of a wide variety of wearable, portable, and lightweight smart devices.”