Fuel cells are devices that generate electricity by harnessing chemical potential energy. All fuel cells possess the same basic configuration, two electrodes (more accurately, a cathode and anode) and electrolyte, however, differ in terms of reactions taking place.
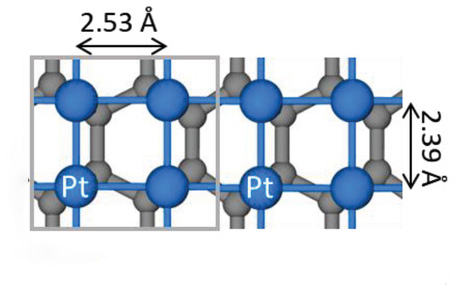
Many experts predict that fuel cells are the answer to a more sustainable means of powering our society, for example, driving long-distance freight traffic. However, one of this technology’s greatest challenges is the high material cost of fuel cell catalysts (electrodes), such as commonly used platinum, which remains a significant problem. This has spurred research efforts find alternative materials or ways of using smaller amounts while maintaining the same catalytic activity.
However, no catalytic fuel cell system that does not rely on platinum has, to date, been found that can achieve the same catalytic activity and the durability.
To address this challenge, a team of researchers from the Georgia Institute of Technology have created several systems that used atom-thick films of platinum supported by a layer of graphene. Their aim is to maximize the total surface area of the platinum available for catalytic reactions, while using as little of the metal as possible.
In most current platinum-based catalyst systems, platinum nanoparticles are chemically bound to a support surface. Here, the surface atoms of the particles do most of the catalytic work, and the atoms beneath the surface play a minor role.
Combined forces between atomic layers
To prepare the atom-thick films, the researchers used a process called electrochemical atomic layer deposition. With this technique, platinum monolayers grow on a layer of graphene, creating samples that had one, two, or three atomic layers. Most striking was the finding that the bond between neighboring platinum atoms in the film essentially combines forces with the bond between the film and the graphene layer to provide reinforcement across the system.
Faisal Alamgir, associate professor at Georgia Institute of Technology explained that typically metallic films below a certain thickness are not stable. However, graphene behaves differently. It is stable in a two-dimensional form, even one atom thick, caused by its very strong covalent directional bonds between its neighboring atoms. Thus, this new catalytic system could leverage the directional bonding of the graphene to support an atomically-thin film of platinum.
“We have already demonstrated that we can run a catalytic reaction from the graphene side of the platinum-graphene hybrid catalyst without sacrificing activity while gaining tremendous stability,” said Alamgir. “What one can imagine now is that we will have catalysts where every atom potentially has two separate active surfaces. While we run a reaction from one side of the catalyst, we can tune the catalytic chemistry from the other side by using an appropriate support material.”
Previous studies on graphene-platinum films have shown that the material behaves similarly in catalytic reactions, regardless of graphene or platinum is the exposed active surface. The team says that future research will include further testing of the behavior of their films in a catalytic environment, and the potential for additional protection of the platinum layer.