Native tissues are complex made up of an extracellular matrix (ECM) containing a variety of cells distributed throughout. The organization and biochemistry of tissues provides for specific regions that cells occupy and are subject to differing mechanical and chemical environments. The complex geometry of such tissues is therefore difficult to mimetic due to the minute local changes in the structure and properties throughout a given tissue type. The structure and properties of native tissues are critical for correct tissue function. Therefore, methods to recapitulate the required complexity of native tissues are important.
Additive manufacturing techniques have been used for this goal to produce such biomimetic constructs for better approaches towards the regeneration of tissues. However, a major problem lies in the low mechanical integrity of soft materials that are used as tissue replicates. Many soft tissues cannot support their own weight during the manufacturing processes. Harder substrates have been used, though are generally relatively hard polymeric materials, to provide support and are removed after gel formation has occurred, and have their own disadvantages. There is a great need for manufacturing processes that produce soft materials for regenerative applications.
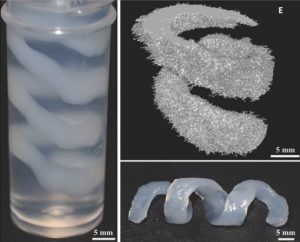
Fabrication of a simple helix loaded with hydroxyapatite nanoparticles and imaged with micro-CT (scale bars = 5 mm). More information here.
Prof. Liam Grover of the School of Chemical Engineering at the University of Birmingham states that ‘inspiration from nature’ is needed to produce complex soft-solid biomimetic tissues. He further adds that as an inspiration from nature, he and fellow researcher Dr. Alan M. Smith of the Department of Pharmacy at the University of Huddersfield, and co-workers, used nature as a basis for a manufacturing method that they recently unveiled in a Communication published in Small. Specifically, Prof. Grover states that supporting materials in nature such as the observation that, “Foetuses are supported by amniotic fluid…and the supporting fluid-gel matrix” was an inspiration to the design strategy behind the process.
The Communication details a method that uses a support material that is self-healing, which enables the penetration of the printing needle into the support bed while printing. The self-healing material supports the part that is being printed. Spontaneous healing of the support material occurs once the needle is retracted. Moreover, this simple method allows easy extraction of the printed material after completion by simply washing away the support material.
The versatility and possibilities of this method are demonstrated by the production of an osteochondral plug, which could be used in the replacement of damaged cartilage. It was also shown that the cells in the cartilage and bone regions maintain their phenotype character. This facile method opens up pathways towards the additive manufacturing of soft and solid tissues, bringing such constructs one step closer to the clinic.